In accordance with the EU's implementation of the Personal Data Protection Act, we are committed to safeguarding your personal information and providing you control over it. We have updated and will regularly update our Privacy Policy to comply with this personal data protection law. Please refer to our latest Privacy Statement.
This website uses cookies to enhance your browsing experience. To learn more about how this website uses cookies, please click here.
Latest News
11.Sep.2024
Selected Articles
Thermoforming Die Cutting Applications & Industry Insights
Ever wondered how all those different shapes of plastic packaging come to life? From drink cups to cookie boxes and cake containers, these everyday items are all made using Thermoforming Die Cutting technology. But what exactly is thermoforming, and how do the tools used in the die-cutting process influence the final product's quality? In this guide, Hung-shuh will break down the essentials of thermoforming and highlight why die-cutting tools are so crucial. By the end, you'll have a clear understanding of the processes that bring these convenient packaging solutions to your everyday life.
The Thermoforming Process: How It Works and Where It's Used
Thermoforming is behind many of the plastic packaging products we use every day. The process starts by heating plastic sheets until they’re soft, then shaping them with vacuum or pressure. Once the plastic cools and takes on its new form, die-cutting tools trim it to the final desired shape. This last step—die-cutting—is critical to ensuring the quality of the finished product. Below, we’ll dive into the details of how this process works and what makes it so essential.Thermoforming Process
-
PLASTIC SHEET ROLL
-
HEATING TO SOFT
-
VACUUM & COOLING
-
UNMOLD
-
ELIMATE EXCESS
-
FINISHED
Thermoforming with Vacuum Forming
1. Mold Creation:
Typically, aluminum alloy or other metal materials are selected to create molds that match the product's shape and size.
2. Material Selection:
Different plastic types are used for various products. For example, PP is used for food packaging, PS for toy packaging, and PET for general commercial packaging. PP is also used for products requiring more durability and rigidity. Therefore, the appropriate plastic material is selected based on specific needs before production.
3. Heating and Shaping:
The plastic material is placed on the mold and heated until it softens. Once the plastic is malleable, vacuum or pressure is applied to make it conform tightly to the mold's surface, creating the desired shape.
4. Cooling and Demolding:
After cooling, the formed product is removed from the mold.
5. Cutting and Shaping:
Using appropriate die-cutting tools, the product is trimmed to retain the necessary parts, with excess material removed to meet design specifications, thus completing the process.
Thermoforming with Vacuum Forming
Thermoforming is a broad process that includes several forming
methods—one of the most common is vacuum forming. In this method,
plastic sheets are heated and then shaped into three-dimensional forms
using vacuum pressure. This technique is widely used for packaging
applications due to its cost efficiency and flexibility.
Die cutting for thermoforming products
Die cutting is essential in shaping thermoformed products. After forming, it trims excess material, ensuring precision and clean edges. This process is crucial for producing accurate, high-quality items.
Features of Thermoforming
Why opt for thermoforming technology? It offers four key advantages:-
Cost Reduction and Efficiency Improvement
-
High Customization
-
Utilizing the Transparency of Plastics for Product Display
-
Dust and Moisture Resistance, Enhanced Product Protection
Application Field | Common Products |
---|---|
Household Item Packaging | Toys, stationery, lampshades, and various household items and packaging |
Food Packaging | Cake boxes, cookie boxes, plastic meal containers, fruit boxes, drink cups and lids, frozen food packaging, etc. |
Medical Packaging |
Pharmaceutical packaging, Press Through Package, disposable medical instruments, surgical trays, protective covers, medical equipment packaging, etc. |
Electronics Industry | 3C products, Consumer Electronics packaging, electronic component trays, etc. |
Hung-shuh's Top 2 Best-Selling Die-Cutting Rule for Thermoforming
In the thermoforming process, while shaping the plastic is crucial, the post-forming cutting step is equally important. If the necessary products aren't cut with precision and finesse, it can result in poor-quality, unrefined packaging. Worse, improper cutting can lead to issues like debris, stringing, or rough edges that might cause injury. Therefore, the cutting stage in thermoforming is a critical aspect of the entire process.To achieve precise and delicate cuts, the die-cutting blades used must be of high quality: they should offer accurate cutting, durability, and customizability (in terms of thickness, hardness, height, or features like perforations or toothed edges). At Hung-shuh, we offer two types of die-cutting blades specifically designed for thermoforming:
TYPE | GR-ground rule | SG-Super ground rule |
---|---|---|
Characteristics |
|
|
Applicable Industries | Widely applicable, often used by clients with moderate or small production needs. | Industries that require high-quality cuts, such as cosmetic, medical,electronic and semiconductor sectors |
Suitable for Cutting | Thermoformed products, films, gaskets, food containers, pharmaceutical boxes, cosmetic boxes, etc. |
Comparison with Other type of cutting rule - Magnified cross-section of PET and Stress Curve Chart
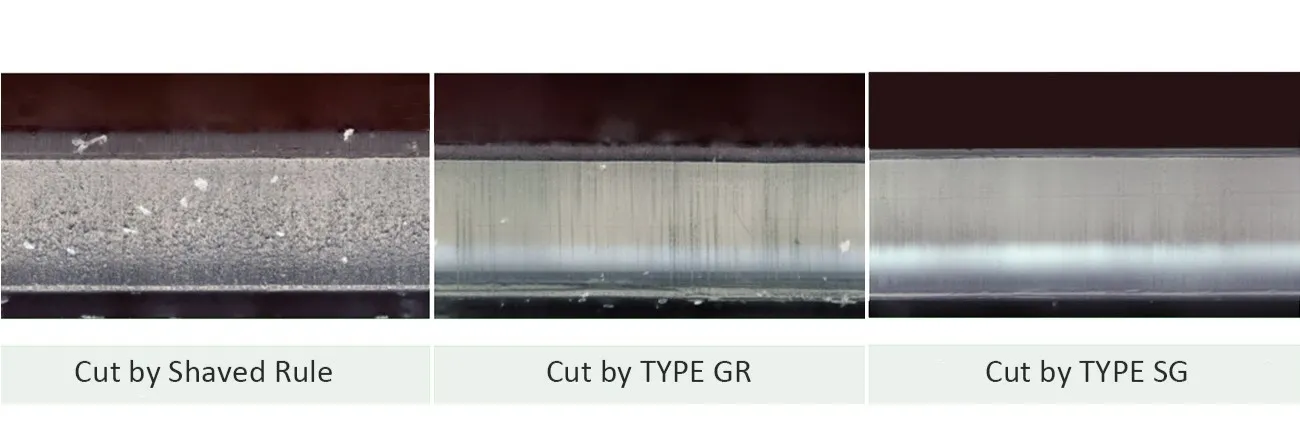
Stress-strain curve
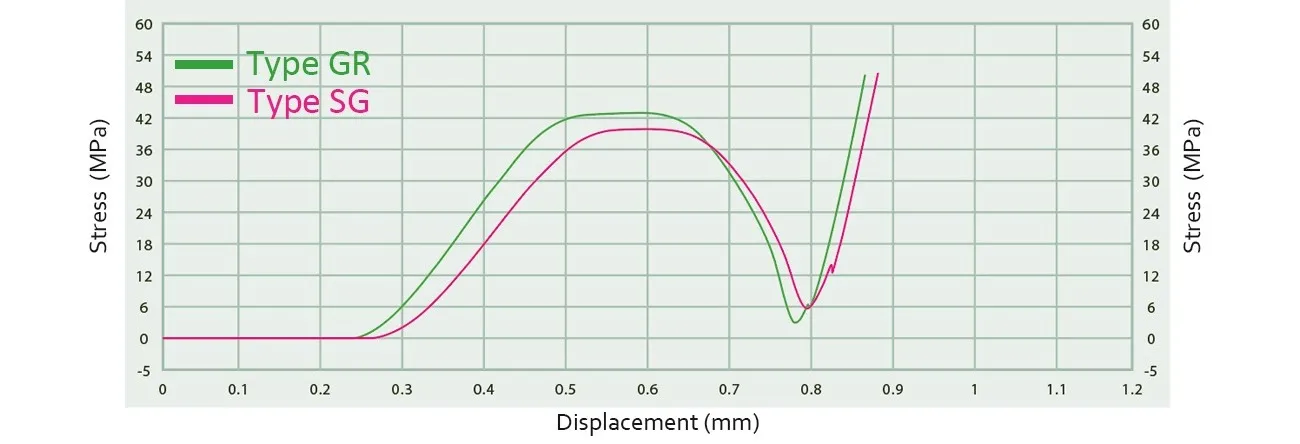
Specifications for TYPE GR and SG
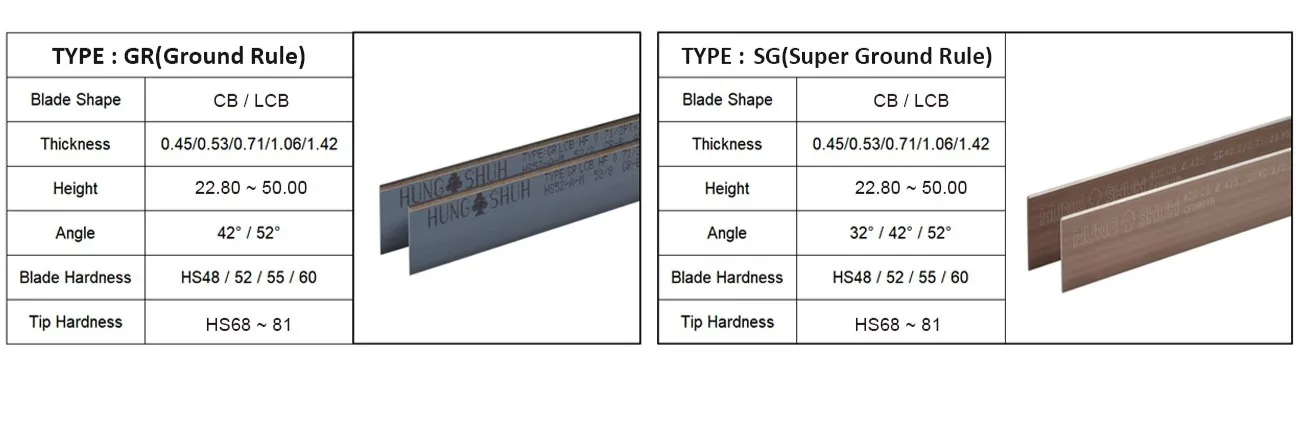
Recommended Die-Cutting Rule for Thermoforming: Hung Shuh Enterprises Co., Ltd.
As one of the top three die-cutting blade manufacturers in the world, Hung Shuh continuously strives for excellence in materials, equipment, and technology. With a craftsmanship-like dedication to professionalism and high quality, we focus on in-depth development in the blade manufacturing field.If your company needs thermoforming die-cutting rules or has related industry requirements, please feel free to contact us.
Other
11
Jun.2025
Selected Articles
Die Cutting Rule Materials & Heat Treatment Technologies
11
Jun.2025
Selected Articles
Die Cutting: Choosing the Best Cutting Rules and Materials
10
Jun.2025
Selected Articles